Vertical Turbine Pumps Promote Sustainable Mining Efforts
Energy is a strategic input for the mining industry in Latin America and worldwide. Mining requires large amounts of energy, which drives up total operational costs. In Chile, mining companies consume 34 percent of the total energy produced in the country and spend approximately 20 percent of their total income on electricity costs.
According to official mining sources, the copper mining industry is expected to consume 41.1 terawatt-hours (TWh) in 2025, an increase of 95.5 percent from 2013. New projects alone will consume 36.2 percent by 2025.
The world’s biggest copper companies use concentration plants—which are energy intensive and use the world’s biggest pumps—as their main production process. In 2013, concentration plants represented 48.6 percent of the total energy consumption for the copper mining industry, which is expected to increase to 64.2 percent by 2025, reaching 26.4 TWh.
Water is another major concern in the mining industry. Freshwater restrictions from scarcity or government policy will have an impact on water availability for future mining projects. Because of these restrictions, desalination plants and seawater pumping systems are also expected to reach 6.2 TWh, representing up to 15 percent of the industry’s total energy consumption.
Pump Stations
Several studies have shown that pumps account for approximately 25 to 32 percent of total motor energy consumption on an average industrial site. Governments from different mining countries are considering applying strict energy efficiency policies to mining companies. These policies will seek significant reductions in carbon emissions and immediate optimizations (up to 10 percent in Chile, the world’s largest copper producer).
In recent years, motor manufacturers have accomplished great results regarding energy efficiency, up to 96 percent. However, this has not been the case for the pump industry. In this new energy-efficient and carbon-reduction scenario, pump designers and manufacturers will play a key role in delivering highly efficient pumps. Energy represents up to 90 percent of a pump’s life cycle cost, making pumps and pump stations a huge opportunity to improve energy efficiency and reduce carbon dioxide emissions in the mining industry.
Vertical Turbine Pumps
Vertical turbine pumps (VTP) are some of the most versatile and reliable pump designs in the turbomachinery industry. Their minimal space requirement, highly efficient semi-axial design and pro-gravity vertical arrangement have made this type pump popular in several industries, particularly mining because of their compact size and ease of maintenance.
In recent years, engineering and design capabilities have improved through mechanical and hydraulic simulation software, advanced manufacturing technologies such as three-dimensional (3-D) printing and computer numerical control (CNC) machining as well as the extensive use of special metallurgies. These changes have allowed pump manufacturers to take this pump type to a new level. Engineers can custom design vertical turbine pumps, such as high-head/capacity pumps or pumps for the transportation of highly corrosive and abrasive fluids for heavy-duty applications, while maintaining the design’s highly efficient characteristics and operational advantages.
Energy-Efficient Pump Design
Hoping to increase its production, one copper producer decided to double its concentration plant’s reclaim water pumping capacity. However, the water quality was a challenge for most pump manufacturers. The water had a high solids content concentration, about 20 percent, and high concentrations of chlorides, about 60,000 milligrams per liter (mg/L).
The company’s previous pumping station consisted of 10 standard short-set vertical turbine pumps with a capacity of 1,500 cubic meters per hour (m3/h) and a total dynamic head of 80 meters (m). Each cast-iron pump had efficiencies below 80 percent. This pump configuration was a poor fit for this highly corrosive and abrasive application, requiring operators to repair and replace these pumps every three to five months.
Assisted by computational fluid dynamics (CFD) and finite element analysis (FEA), a pump manufacturer custom designed a vertical turbine pump that met all the requirements for this abrasive service (see Image 1).
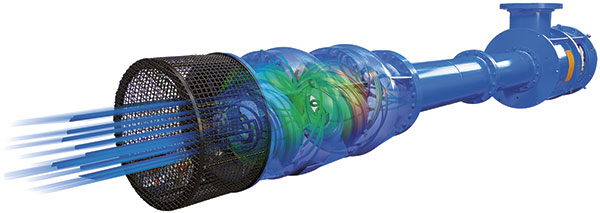
The pump was designed for a capacity of 3,100 m3/h and a total dynamic head of 90 m, obtaining an efficiency of 85 percent. Because of the highly abrasive potential of the water, the pump was designed to run at a low speed of 995 rotations per minute (rpm) or 50 hertz. The low speed diminished the abrasive wear of its internal parts, which in the case of centrifugal pumps, is known to be proportional to the cube of the particles’ flow velocity.
Because the pump was for a short-set application, some special design considerations were necessary to guarantee reliability and long operational life. All the bearings and wear rings use advanced polymeric materials with better lubrication properties. An independent axial thrust bearing assembly supports the pump’s thrust and protects the motor from any damage during startup and operation. Flanged column pipes ensure pump and shaft straightness during operation. A reinforced suction bell and strainer minimize suction submergence and prevent the entrance of large solid particles.
To protect the pump from the highly corrosive and abrasive water, duplex 2205 stainless steel was specified for all the wet parts of the pump design. This material is a combination of austenitic and ferrite stainless steel. It is ideal for chloride-containing environments because of its resistance for localized corrosion types such as intergranular, pitting and crevice. Because of this feature, it provides a better performance than 316L or 317L stainless steels. It is also resistant to chloride stress corrosion cracking (SCC), so it was the right choice for this highly corrosive application (see Image 2).
High resistance to fatigue, abrasion and erosion also made the material suitable for this project. Its combination of moderate hardness and high toughness is ideal for the pumping of water with high solid concentration.
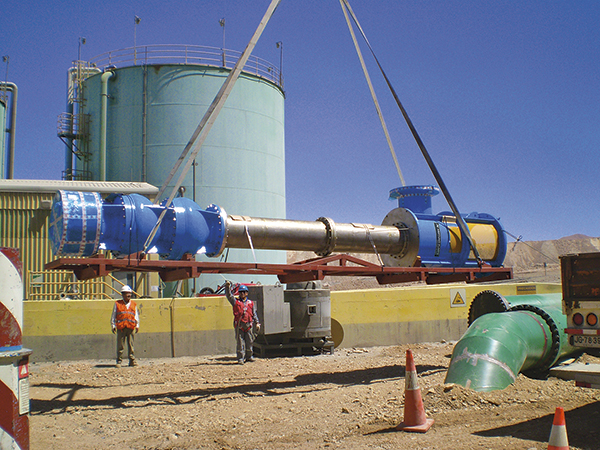
The internal geometry of this CFD-validated pump design was then 3-D printed directly from the 3-D computer-aided design (CAD) files to strictly maintain all of its mechanical and hydraulic characteristics, which ensure its highly efficient performance. This 3-D printed pump model was cast using advanced investment casting technologies by the pump manufacturer in-house to guarantee perfect reproduction and a smooth surface finish, both significant factors when striving for high efficiency.
The pump was then assembled and tested. Results showed that the error between CFD simulation and the actual pump performance test was lower than 3 percent. This was well within the 5 percent allowable tolerance that ISO 9906 for pump performance tests specifies for efficiency in its Grade 2B.
The installation of these pumps allowed the end user to double reclaim water pumping capacity, reaching approximately 31,000 m3/h, with 50 percent fewer pumps than would have been required with the previous pump model. The new model increased the user’s system reliability with a heavy-duty metallurgy capable of withstanding this highly abrasive and corrosive application for 10 to 12 months before repairs or replacement become necessary. The pump system efficiency showed an improvement of approximately 5 percent, reducing energy costs as well as carbon dioxide emissions to the atmosphere (see Image 3).
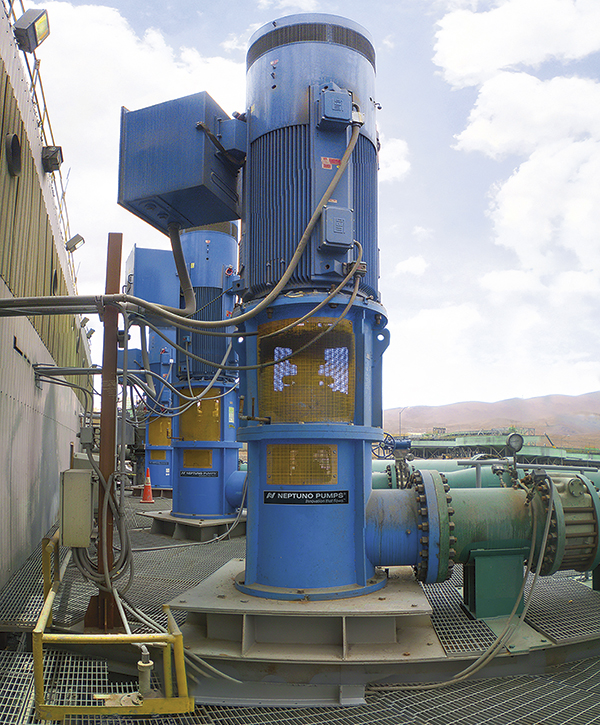
Sustainable Mining
Energy efficient vertical turbine pumps are the future for the mining industry because they address two major issues for today’s sustainable mining: energy and water. New design and manufacturing technologies, such as CFD/FEA simulations and 3-D printing, play a key role in delivering energy-efficient vertical turbine pumps. These pumps can help mining companies operate sustainable processes and save them money by improving their system’s reliability and reducing energy costs. They also demonstrate a focus on the environment and the mine’s surrounding communities by reducing the carbon emissions of the pumping systems across their entire process.